Lyophilized Microspheres and Bulk Freeze Drying: Breakthrough Technology. Breakthrough Advantages!
MERIDION Technologies offer you new opportunities:
- Product Innovation
- Manufacturing Flexibility
- Process Robustness
- Total Containment
- Significant Cost Reductions
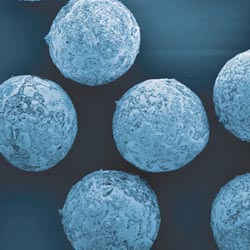
Manufacturing flexibility and cost savings
Filling of lyophilized product on demand
- Filling quantities as required
- Contained product handling by gravity: no need for loading and unloading systems in sterile area
- Vial/final recipient flexibility: no specific freeze drying requirements for primary packaging
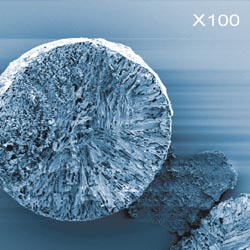
Innovation & formulation flexibility
- Multicomponent formulations achieved by combining different lyophilized products in the final recipient (vial), e.g. to overcome incompatibilities
- Further modifications of product properties esp. in the area of Solid Dosage Forms like ODTs, Fast Dispersible Formulations, by applying known technologies so far not applicable to lyophilized compounds
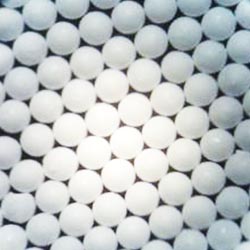
MERIDION SprayCon: Spray Freezing of Microspheres
Frozen microspheres are generated by dispersing the substrate liquid using high precision nozzles into monosized single droplets, which by gravity pass through a cooling zone, congealing to frozen spheres.
- Narrow particle size distribution
- Size selectable from 250 µm – 800 µm
- After freeze drying, the product
- is homogeneous,
- has excellent flow properties
- is dust free
Product innovation
- Further processing of the lyophilized spheres, e.g. by coating or by combination of products is possible
- Highly cost effective utilization of cooling energy – no direct contact with primary cooling agent
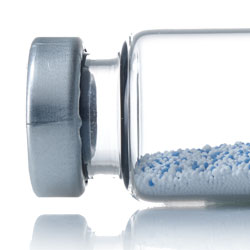
MERIDION LyoMotion: Dynamic Bulk Freeze Drying
In the dynamic freeze drying process, flowable bulkware is lyophilized in a rotational freeze dryer under constant gentle mixing. Sublimation energy is transferred by radiation and temperature controlled surfaces.
MERIDION LyoMotion: Advantages and characteristic features
MERIDION LyoMotion: Advantages and characteristic features
Product quality
- Homogeneous, dust free product due to constant and gentle mixing – no caking, no variations in product density
- Direct monitoring of product temperature
Up to 50% reduced drying times by
- maximized heat and mass transfer (entire particle surface available)
- heat transfer directly to the product
- maximized flow of vapor – no limitation by stoppers or diffusion barriers of larger product layers
Process robustness
- Direct monitoring of product relevant parameters
- OOS results reduced
- PAT tools directly accessible
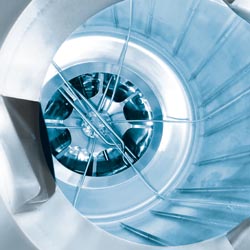